Diamond Lapping Film: The Ultimate Precision Polishing Solution
What Is Diamond Lapping Film?
Diamond lapping film is a high-performance abrasive material designed for ultra-precise surface finishing. It consists of micron-graded diamond particles uniformly coated on a polyester film backing. Known for its superior cutting ability and durability, diamond lapping film is widely used in industries requiring high precision, such as fiber optics, semiconductors, ceramics, metalworking, and electronics.
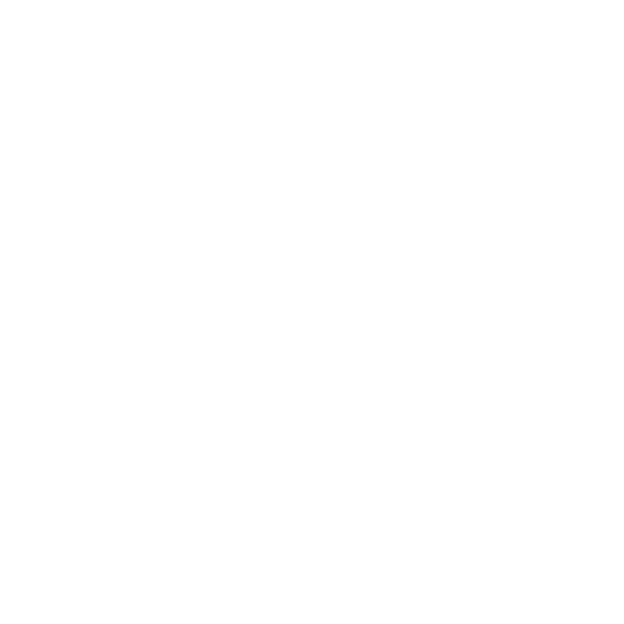
Here's a breakdown of its key characteristics and applications:
Key Features:
· Abrasive Material:
o It utilizes diamond particles, which are the hardest known material, as the abrasive. This makes it ideal for working with extremely hard substances.
· Precision:
o The diamond particles are precisely graded in size (measured in microns), allowing for very controlled and predictable material removal.
· Backing Material:
o The diamond particles are bonded to a flexible backing material, typically a polyester film.
· Versatility:
o It's available in various grit sizes and formats (sheets, rolls, discs) to suit different applications.
Common Applications:
· Fiber Optics:
o Essential for polishing the ends of optical fibers and connectors, ensuring optimal signal transmission.
· Semiconductor Manufacturing:
o Used for precision finishing of semiconductor wafers and other electronic components.
· Metalworking:
o Employed for sharpening tools, polishing hard metals, and achieving very fine surface finishes.
· Ceramics and Hard Materials:
o Ideal for polishing and finishing ceramics, glass, and other hard materials.
· Precision Engineering:
o Used in any application requiring very high levels of surface finish and dimensional accuracy.
Key Advantages:
· High Material Removal Rate:
o Diamond's hardness allows for efficient material removal.
· Exceptional Surface Finish:
o Produces extremely smooth and highly polished surfaces.
· Long Lifespan:
o Diamond's durability extends the lifespan of the lapping film.
When using diamond lapping film, it's often recommended to use a lubricant or coolant to improve performance and extend the film's lifespan.
Available Grit Sizes of Diamond Lapping Film
Diamond lapping films are available in a wide range of micron sizes, from coarse grinding to ultra-fine polishing.
Micron Size | Grit Equivalent (FEPA) | Common Use |
---|
45 µm | ~320 | Rough material removal |
30 µm | ~500 | Pre-polishing or shaping |
15 µm | ~1000 | Intermediate polishing |
9 µm | ~1500 | Connector end-face preparation |
6 µm | ~2500 | Pre-final finish on metals & ceramics |
3 µm | ~8000 | Final polishing of hard materials |
1 µm | ~14000 | Near-mirror finish on fiber optics |
0.5 µm | ~60000 | Ultra-fine final polishing |
0.1 µm | Sub-nanometer | High-end precision and defect analysis |
Each grade ensures uniform removal, reduced scratches, and enhanced surface quality.
Use of Diamond Lapping Film
1. Fiber Optic Connector Polishing
Used to polish ferrules and end-faces of MPO, LC, SC, ST connectors.
Essential for meeting industry standards for insertion loss and return loss.
Common grit sequence: 30 µm → 9 µm → 3 µm → 1 µm → Final film (0.1–0.3 µm).
2. Semiconductor & Microelectronics
Ideal for cross-section analysis of silicon wafers, ICs, and packaging.
Produces scratch-free surfaces for failure analysis and microscopy.
Enables sub-micron finishing on Si, GaN, sapphire.
3. Metallographic Sample Preparation
Used to polish hard metals like tungsten carbide, stainless steel, and tool steels.
Replaces traditional lapping compounds with more consistent, cleaner performance.
4. Ceramic and Glass Polishing
Enables defect-free, mirror-like finish on zirconia, alumina, and optical glass.
Ideal for anilox rollers, precision rods, and seals.
5. Other Industrial Uses
Formats & Backings Available
Diamond lapping film is typically available in:
Sheets: 8.5” x 11”, 9” x 11”
Discs: 4", 5", 6", 8" diameters
Rolls: 50m or 100m lengths
Adhesive or PSA backings, or plain film
Custom die-cut shapes for automated polishing machines
Why Choose Diamond Lapping Film?
Extreme hardness = Fast and efficient cutting of difficult materials
Micron precision = Tight tolerances and predictable performance
No slurry mess = Cleaner than traditional lapping with pastes
Long-lasting = Reduces total cost over time
Best Practices
Use in progressive grit sequence to avoid deep scratches.
Apply consistent pressure and proper backing pad.
Clean substrate between grit changes to avoid contamination.
Store in dust-free environment to preserve film quality.
Conclusion
Diamond lapping film is the go-to solution for anyone needing high precision, reliable surface finishing, and long-term performance. With a full range of grit sizes and applications, it supports everything from fiber optic connector polishing to high-end microelectronics and ceramic finishing.